Continuous bioprocessing, already conventional in many manufacturing fields, has established itself in biopharma, which is beginning to realize continuous processing’s compelling advantages, such as enhanced product quality, greater efficiency, and rapid scalability. Continuous bioprocessing has been proposed as one future biomanufacturing state because it operates at similar scales for both clinical and commercial production using flexible facilities that can react readily to changing market pressures. Owing to the growing demand for innovative and complex therapies and expanding competition among biopharmaceutical manufacturers, there has been a shift from batch to continuous manufacturing. Although batch manufacturing is the most preferred manufacturing method, considering the commercial advantages of continuous manufacturing, it is witnessing increased adoption in the pharmaceutical industry. Some of the advantages of continuous manufacturing include:
- Reduction in the operational, running, and environmental costs: A continuous bioprocessing facility is at least 70% smaller than a batch production facility. Thus, a reduction in facility and equipment size helps in saving operational costs.
- Ease of scaling-up in continuous processing: In continuous bioprocessing, identical equipment is used during the process development for production scale, eliminating validation issues, and enabling cost savings.
- Increased profitability: Continuous processing enhances profitability in two ways: 1) by allowing more efficient and economical facility design and utilization, and 2) by reducing the cost of goods through reduced footprint and lower media and energy consumption, enabling increased automation with a consequent reduction in service requirements and operator time.
- Personalized medicine: The rise in the adoption of single-use technologies to manufacture personalized medicines in the continuous process quickens the supply chain, boosts productivity, and eliminates the risk of contamination.
- The integration of measuring equipment and real-time sensors with continuous manufacturing equipment enables feedback control and continuous monitoring. The continued generation of process data allows manufacturers to improve processes by analyzing the data. Along with providing better quality products and enhanced productivity, real-time process control supports the FDA’s quality-by-design (QbD) approach to manufacturing
These advantages have led to significant investments in continuous bioprocessing.
- In December 2018, WuXi Biologics (China) invested USD 357 million in Ireland to set up a new biologic manufacturing facility featuring single-use bioreactors for commercial biomanufacturing, compatible with continuous bioprocessing.
- In November 2018, Innovate UK granted USD 1.85 million to a partnership of Cell and Gene Therapy Catapult (U.K. based research and technology organization), international CDMO—Cobra Biologics (U.K.), and Pall Corporation (U.S.) to investigate continuous bioprocessing of adeno associated virus for gene therapy applications
The U.S FDA is encouraging pharmaceutical manufacturers to adopt continuous manufacturing. In February 2019, the U.S. FDA made available the draft regulatory guidance for continuous manufacturing. It provides information regarding its current idea on the quality considerations for continuous manufacturing of small molecule and solid oral drug products regulated by the Center for Drug Evaluation and Research. Many proponents of continuous manufacturing technology, including GlaxoSmithKline plc. (U.K.), Johnson & Johnson (U.S.), and Vertex Pharmaceuticals, NC. (U.S.) are helping the FDA develop the right environment to foster continuous manufacturing on a wider scale.
As estimated in a research study, continuous manufacturing has a large cost-reducing potential. Continuous manufacturing estimated capital expenditure could be lower between 20% to 76%. Overall, the cost would be 9% to 40% lower in a continuous manufacturing facility.
Public-private partnerships and supportive initiatives boosting innovations in biopharmaceutical manufacturing are further driving the market growth. In January 2019, the National Institute for Innovation in Manufacturing Biopharmaceuticals (NIIMBL) revealed 22 new projects and funding for advancing biopharmaceutical manufacturing. The new projects revealed have an approximate value of USD 13 million. In August 2019, NIIMBL selected 15 new technology and talent development projects to advance biopharma manufacturing. In May 2020, NIIMBL announced USD 10 million funding for advancing biopharma manufacturing innovations.
Thus, supportive initiatives for the adoption of continuous manufacturing, recent investments in continuous manufacturing, and continuous manufacturing advantages are driving the market growth. The global continuous bioprocessing market is expected to grow at a CAGR of 23.0% to reach USD 348.9 million by 2027, according to Meticulous Research®.
Related Tag:
Related Blogs:
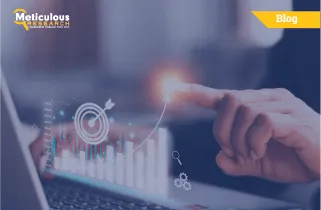
NGS Services: Accelerating Cancer Research
Read More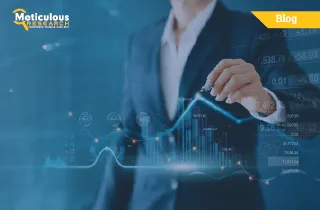
Home-Care Products: A Boon for Sleep Apnea Patients
Read More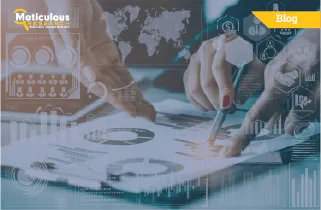
The Importance of Viral Vaccines
Read More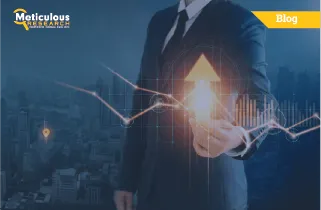
What’s Happening with Neurogenomics Research in China Today?
Read More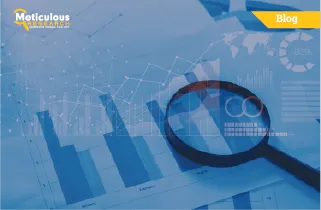
IVD Assay Development Market: Key Insights
Read More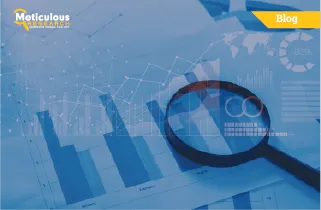
NGS: Advancing Genomics & Biotechnology in Saudi Arabia
Read More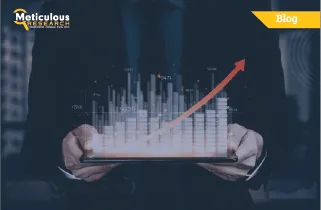
Scope of Microarray in Multiple Industries in China
Read More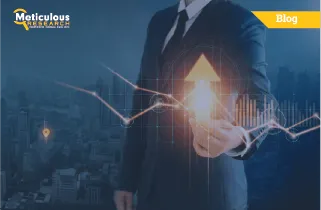
DNA Sequencing Market: Unlocking the Potential
Read More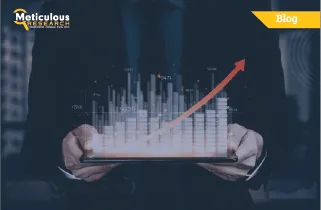
Parenteral Nutrition: A Life Saving Form of Nutrition
Read More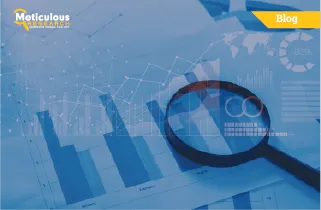
The Impact of Clinical Lab Automation on Healthcare Efficiency
Read More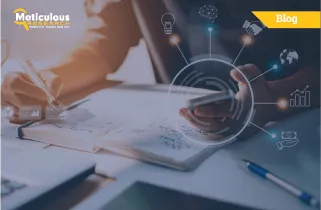
Remote Patient Monitoring: A Comprehensive Overview
Read More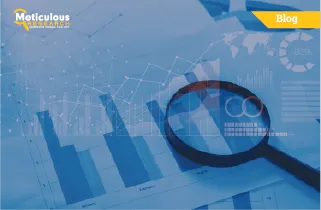
Electrosurgery: A Comprehensive Overview
Read More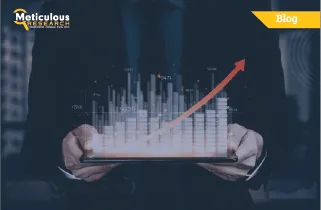
Genomics: A Revolution in Diagnostics & Drug Discovery
Read More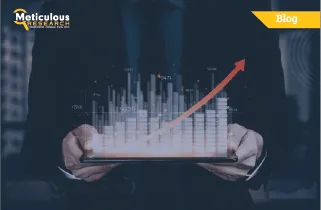
Importance of Automation In Streamlining Laboratory Workflows
Read More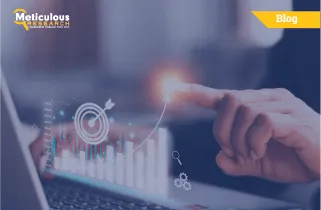
Bioinformatics: Primary Basis of Analytics in Genomics Research
Read More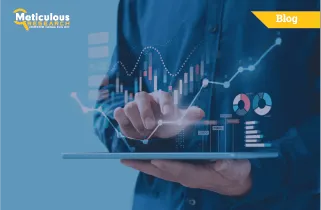
Sample Preparation Market: To Achieve Optimized Sample Analysis
Read More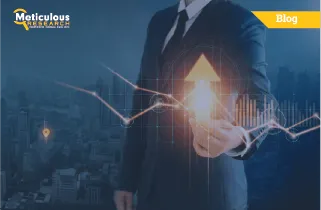
Sequencing Kits: The Key to Unlock Genomic Insights
Read More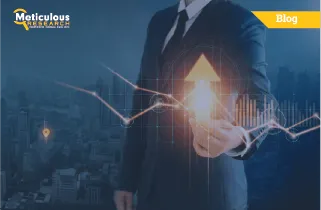
NGS Services: Accelerating Cancer Research
Read More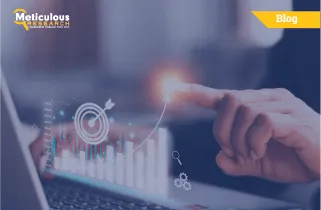
NGS Services: Accelerating Cancer Research
Read More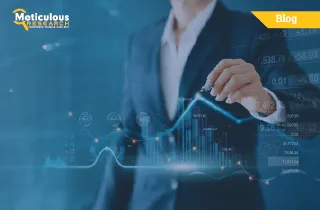
Home-Care Products: A Boon for Sleep Apnea Patients
Read More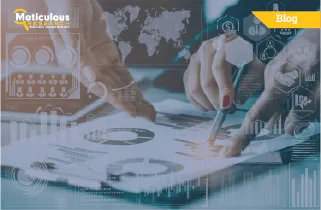
The Importance of Viral Vaccines
Read More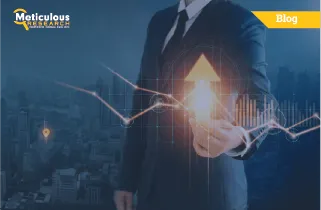
What’s Happening with Neurogenomics Research in China Today?
Read More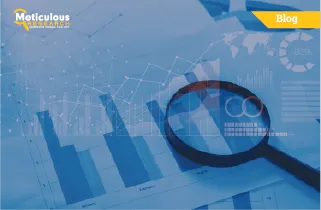
IVD Assay Development Market: Key Insights
Read More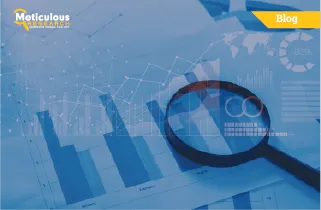
NGS: Advancing Genomics & Biotechnology in Saudi Arabia
Read More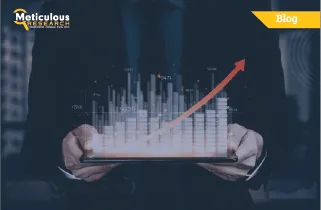
Scope of Microarray in Multiple Industries in China
Read More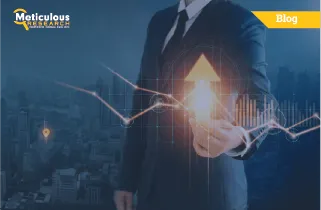
DNA Sequencing Market: Unlocking the Potential
Read More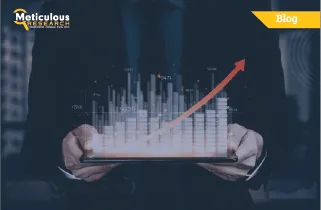
Parenteral Nutrition: A Life Saving Form of Nutrition
Read More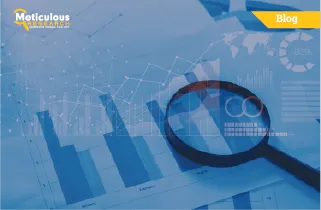
The Impact of Clinical Lab Automation on Healthcare Efficiency
Read More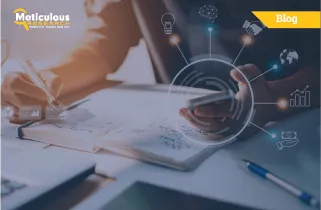
Remote Patient Monitoring: A Comprehensive Overview
Read More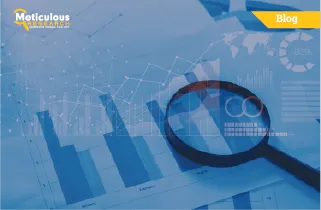
Electrosurgery: A Comprehensive Overview
Read More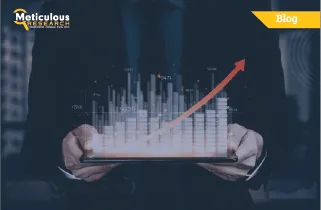
Genomics: A Revolution in Diagnostics & Drug Discovery
Read More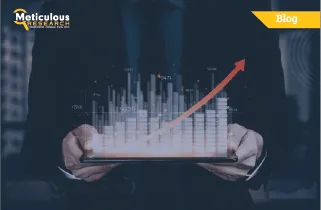
Importance of Automation In Streamlining Laboratory Workflows
Read More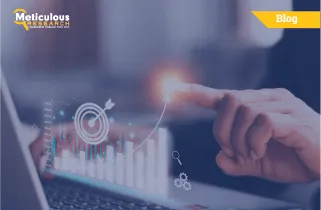
Bioinformatics: Primary Basis of Analytics in Genomics Research
Read More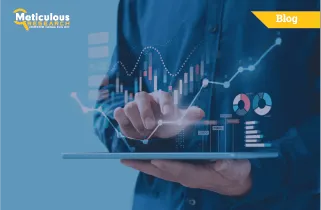
Sample Preparation Market: To Achieve Optimized Sample Analysis
Read More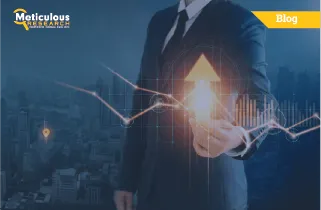
Sequencing Kits: The Key to Unlock Genomic Insights
Read More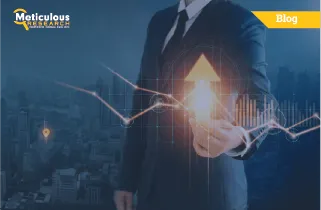
NGS Services: Accelerating Cancer Research
Read More