In recent years, the adoption of electric vehicles (EVs) has increased due to stringent government regulations for phasing out fossil fuel-powered vehicles, government investments in improving public EV charging infrastructure, and incentives for EV adoption such as subsidies and tax rebates. Welding is crucial in the automotive industry as it is directly related to passenger safety. Moreover, clean and strong welds are important as they improve the appearance and reliability of vehicles. The most commonly used welding methods for automotive applications include resistance spot welding (RSW), resistance seam welding (RSEW), metal inert gas (MIG) welding, tungsten inert gas (TIG) welding, laser beam welding (LBW), friction welding (FW) and plasma arc welding (PAW).
The benefits of automated welding for the automotive industry are as follows:
- Robotic welding can dramatically increase the safety of automotive workshops. It can be used in hazardous environments where human welders might be exposed to chemicals, fumes, extreme heat & noise, and weld flash. Robotic welding also helps keep workers healthy and safe by limiting their chances of experiencing musculoskeletal stress caused by lifting or twisting.
- Automated welding can complete tasks more quickly and consistently than manual labor while meeting industry standards. Additionally, robotic welding can produce tighter welds and perform highly intricate tasks, making it more efficient than human welders.
- Welding automation can also help manufacturers reduce waste. Automated welding reduces both scrap and consumable costs. Scrap reduces as there are no fatigue-induced errors, and the use of consumables drops because robots only use the required quantity of filler every time.
Moreover, increasing initiatives by OEMs and market stakeholders launched various welding robots, supporting the demand for robotic welding in various industries. For instance:
- In 2021, Trio Motion Technology (England) launched a range of SCARA robots. The launch provides OEMs with robot control, motion control, and machine automation from a single controller. Trio's SCARA robots have been designed for applications including pick and place, welding, assembly, and dispensing, making the range suited to electronics manufacturing (3C), packaging, and material handling.
- In September 2020, Korean automotive supplier Seojin Industrial Co., Ltd (South Korea) chose KUKA AG (Germany) to deliver approximately 185 robots from the KR QUANTEC series for adoption in handling and welding tasks in Korea. Such developments are expected to drive overall market growth.
- In March 2020, Fronius International GmbH (Austria) launched its Fronius welding torches for manual Tungsten Inert Gas welding (TIG), which can be customized to suit the welder's preferences as well as the welding task. Similarly, in March 2019, Boostweld launched the SWIFT series MIG welding torch. The SWIFT features gas flow technology that delivers an unprecedented increase in efficiency, saving 70% shielding gas at optimum velocity compared to the most popular MIG welding torches.
- In December 2019, Yaskawa Electric Corporation (Japan) launched its two types of horizontal articulated SCARA robots: MOTOMAN-SG400 (payload capacity: 3kg, maximum reach: 400mm) and MOTOMAN-SG650 (payload capacity: 6kg, maximum reach: 650mm), specifically for the assembly and transportation process of small components.
Such initiatives by the OEMs help generate the demand for the robotic welding market during the forecast period.
Access Free Report Here: https://www.meticulousresearch.com/download-sample-report/cp_id=5303
Related Tag:
Related Blogs:
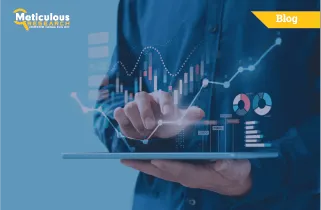
Technological Trends in Air Conditioners Market
Read More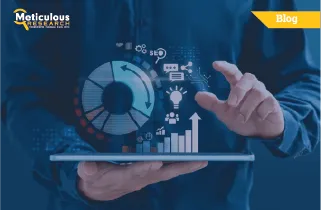
Rising Investments and Advancements in the LiDAR Market
Read More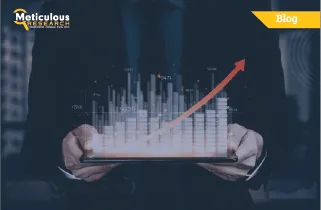
Increasing Adoption of Robots in the Manufacturing Sector
Read More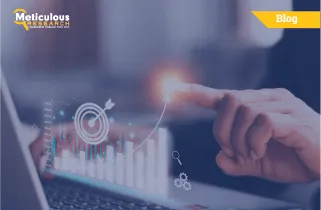
3D Printers Market
Read More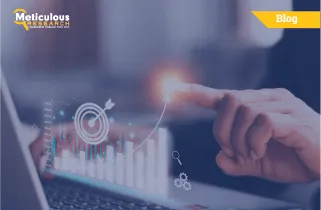
Solid-State Batteries Market
Read More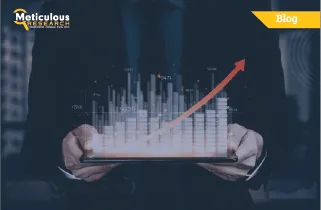
Surging Demand for Smart Sensor-enabled Wearable Devices
Read More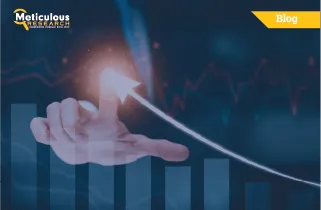
3D Machine Vision Meets Industry 4.0
Read More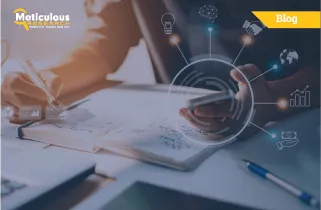
Optoelectronics – A Promising Technology
Read More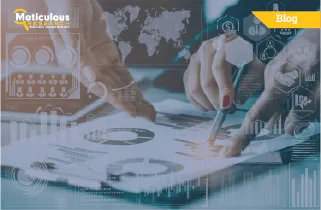
Increasing Utilization of Archimedean Screw Pumps in Sewage Treatment
Read More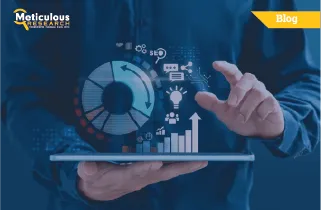
Transformative Potentials of 3D Food Printing
Read More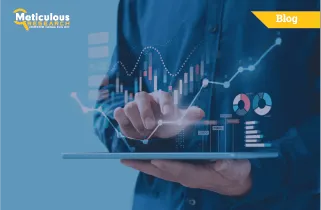
Technological Trends in Air Conditioners Market
Read More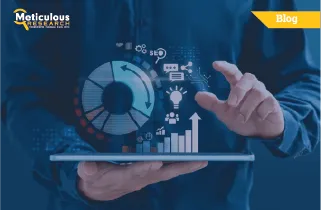
Rising Investments and Advancements in the LiDAR Market
Read More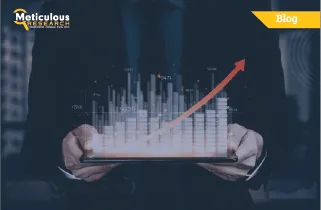
Increasing Adoption of Robots in the Manufacturing Sector
Read More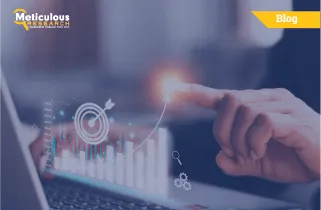
3D Printers Market
Read More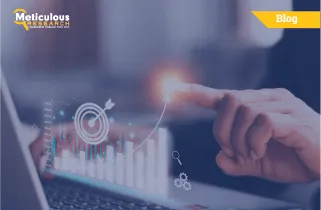
Solid-State Batteries Market
Read More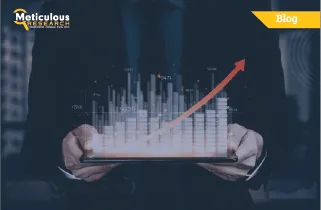
Surging Demand for Smart Sensor-enabled Wearable Devices
Read More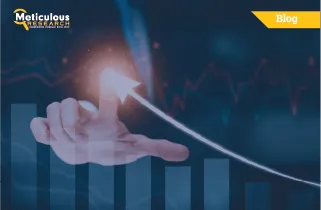
3D Machine Vision Meets Industry 4.0
Read More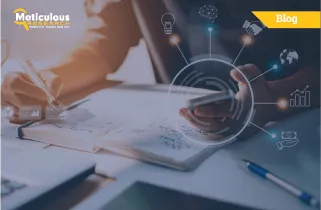
Optoelectronics – A Promising Technology
Read More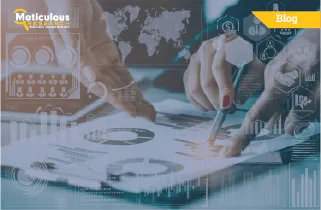
Increasing Utilization of Archimedean Screw Pumps in Sewage Treatment
Read More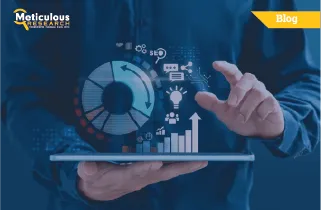
Transformative Potentials of 3D Food Printing
Read More